As the name implies, and FPV Drone Power Distribution Board (PDB) is a printed circuit board that is used to distribute the power from your flight battery to all different components of the multirotor. Prior to PDB’s becoming common it was necessary to connect all the different components using wire and the result often resembled an octopus and weighed a considerable amount due to the amount of copper and solder joints in the wires.
There are many different PDB’s available from various manufacturers, the majority of them provide very similar features. Initially PDB’s were very simple and were just a thick copper PCB with an input and multiple outputs. As the need for regulated voltages for various components has become more common, manufacturers have begun including voltage regulators on the PDB so that voltage sensitive components can be fed reliable, stable, and clean power. This is especially important when dealing with video components that are often sensitive to electrical noise generated by the motors and ESC’s during flight.
PDB’s are one of the simplest components on a Multirotor and therefore are one of the easiest to choose. There are 3 main points that should be considered when choosing a PDB for your multirotor:
- Size and layout
- Voltages and Current Capability (on board voltage regulators)
- Additional features
It is necessary to have a good idea of what parts you will be using in your multirotor build in order to make sure that you choose a PDB that will have the right features and be able to support the power consumption of all the components.
FPV Drone Power Distribution Board Size and Layout
Size is relatively straight forward, however is worth mentioning because PDB’s come in all shapes and sizes. Some are made specifically for certain frames while the majority use a 30×30 standardised mounting.
Depending on the frame you have chosen, there may be a custom PDB available which may replace a Carbon component in the frame and greatly simplify the wiring and cleanliness of the build. If your frame does not have a dedicated PDB available, you need to choose one that will suit your intended build. This is where it is necessary to have a good idea of what other components you intend to use.
Look at the layout of the pads on the PDB and check if they are in places that make sense for how you would like to orient the components in your build, if you choose a FPV Drone Power Distribution Board with the layout that most closely resembles your intended build, then the final result will be as clean and lightweight as possible. If you choose one with a poor layout, you will end up with lots of wires running across the board and some of the benefits of having a PDB will be lost.
One of the most important features of the layout to consider is where the ESC wires will connect, after the main battery wires, these are often the thickest and heaviest wires on the multirotor and if you can keep these as short as possible, your build will be lighter. Usually look for PDBs that have the ESC wire pads near the corners for the cleanest build.
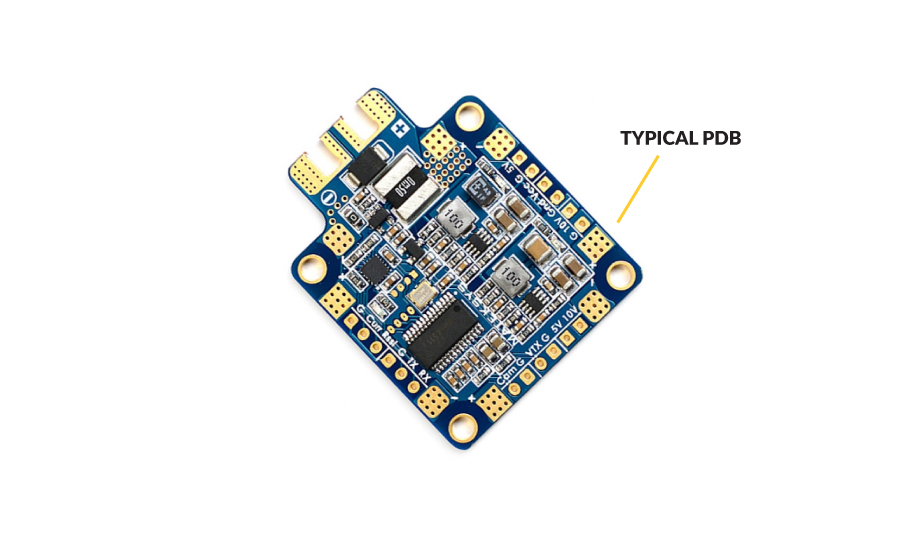
Voltages and Current Capability (On Board Voltage Regulators)
When choosing a PDB you need to find out what voltages your components require, and make sure that the PDB you choose has a regulator for those voltages on board. By doing this your build will be as clean as possible, both aesthetically and electrically. Typical components that can require specific voltages are the FPV Camera, Video Transmitter (VTX), Reciever and optional extras like LED’s.
Voltages
Be aware some receivers require 3.3v while others require 5v. Some popular VTX’s are limited to 5v and others can be limited to 12v input which must be regulated if you intend to use a 4S 14.8V flight battery. VTX’s that can handle voltage directly from the flight battery are becoming more common, so it is important to check (see the article about VTX’s by clicking here).
Another thing to consider when choosing a PDB is the features of the flight controller (FC) you are planning to use, many FC’s now include voltage regulators for the receiver (RX), if the FC you are going to use offers a regulator for the receiver, there is no need to have two in your multirotor build. Also pay attention to what the input voltage for the FC is, some FC’s will now accept battery voltage and take care of regulating the voltage to internal components which means that you may not need a 5V output on your FPV Drone Power Distribution Board.
Current Capabilities
The amount of power that a voltage regulator on a PDB can supply is often limited by the size of the components used and it is very important not to exceed the maximum rated current otherwise the voltage regulator can overheat and will most likely be damaged. This is very dangerous as this can often happen while flying and the components connected to the voltage regulator will stop working, this can often lead to complete video failure or loss of control.
When choosing a suitable FPV Drone Power Distribution Board you will see that the available output voltages are usually accompanied by a number in brackets ie, 12v (2A) this is referring to the maximum current output of that voltage regulator. The capital A stands for amps and eac amp is 1000mA, mA stands for milliamps. You should check the other components you plan to connect to the regulator to see how much power they require, this will often be given in mA either on the packaging or on the products website. It is good practice to make sure the amount of power required from the voltage regulator does not exceed 80% of the regulators rated power output.
VTX’s are often the most power-hungry components on a multirotor, especially when used at higher powers. LED’s also consume a surprisingly large amount of power so make sure you check the current required for these components.
FPV Drone Power Distribution Board Additional Features
Some manufacturers will offer additional features on their PDB’s, this can range from built in LED lighting or buzzers to onboard microphones for capturing the audio from the multirotor so that it can be transmitted back to the goggles along with the video feed. Sometimes choosing a PDB with any of these features built in can reduce the wiring and complexity of your multirotor making it easier to build and have less potential failure points.
FC / PDB’s
Recently more manufacturers are offering PDB’s built directly into the flight controller (FC) this greatly simplifies a multirotor build and allows the FC to have easy access to power consumption information which depending on the FC/PDB chosen may allow you to monitor the power consumption of your multirotor in real time, making it easier and more accurate to gauge the amount of battery used and allow you to optimise your flight times depending on the size of the battery used. Using an FC/PDB also means it is possible to use only one board in the multirotor flight controller ‘stack’. This is very helpful in tight or low profile builds and is becoming much more popular in the micro multirotor markets.
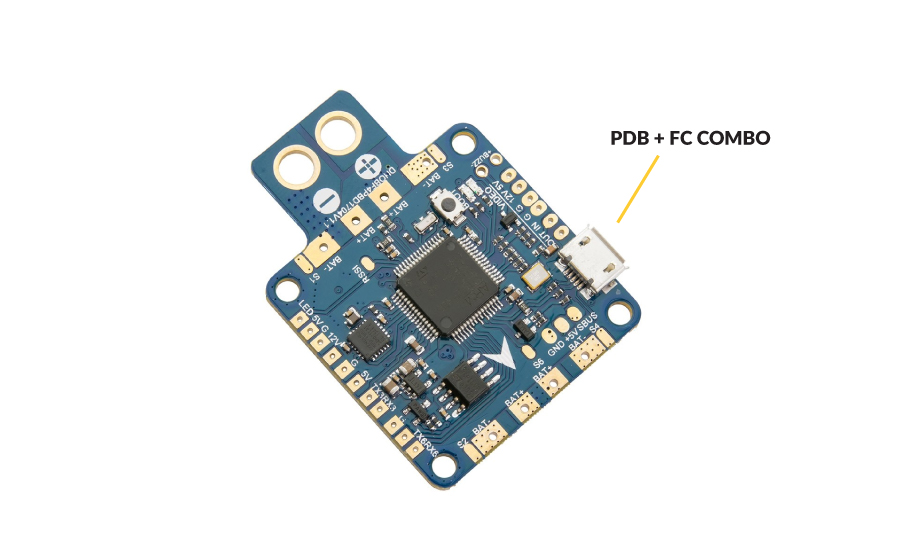
Conclusion
Hopefully this article has helped explain the main points to consider when choosing a PDB for your multirotor build. There are many options available so take the time to shop around. As always looking up reviews or explanatory videos for the products you are considering can be a great way to better understand the features and capability before you make your purchase.